The Essentials of Pressure Calibration: Ensuring Accurate Measurements
- cciaustralia01
- Aug 6, 2024
- 3 min read
In many industries, accurate pressure measurement is critical for ensuring safety, efficiency, and compliance with regulations. Calibration is the process of verifying and adjusting the accuracy of pressure measurement devices to ensure they perform reliably.
This blog explores the importance of pressure calibration, how it works, and why it matters for your operations.
This process is vital for devices like pressure gauges, transmitters, and sensors that measure the force exerted by a fluid (liquid or gas) on a surface.
Why is Calibration Important?
Safety: Accurate pressure measurements are crucial for safety in many applications. In industries like oil and gas, pharmaceuticals, and manufacturing, incorrect pressure readings can lead to equipment failure, leaks, or hazardous conditions. Regular calibration ensures that pressure instruments provide reliable data, reducing the risk of accidents.
Compliance: Many industries are subject to strict regulatory standards that require regular calibration of pressure measurement devices. Compliance with these standards helps avoid legal issues and ensures that your operations meet industry requirements.
Operational Efficiency: Accurate pressure readings contribute to efficient process control and product quality. Inaccurate measurements can lead to inefficiencies, increased operational costs, and compromised product standards.
How Does Calibration Work?
Preparation: The first step in pressure calibration is preparing the calibration equipment. This typically involves setting up a pressure source (such as a calibration pump or test bench) and ensuring that the calibration standards (like reference gauges or sensors) are in good working condition.
Comparison: The device under test (DUT) is exposed to a series of known pressure values from the pressure source. The readings from the DUT are compared against the reference standards to determine its accuracy.
Adjustment: If discrepancies are found, adjustments are made to the DUT to correct any inaccuracies. This may involve recalibrating the device or making mechanical adjustments to ensure it provides accurate readings.
Verification: After adjustments, the DUT is tested again to verify that it meets the required accuracy standards. The calibration process is complete once the device consistently provides accurate readings.
Documentation: Calibration results are documented, including details of the equipment used, the pressures tested, and any adjustments made. This documentation serves as a record of compliance and can be useful for future reference.
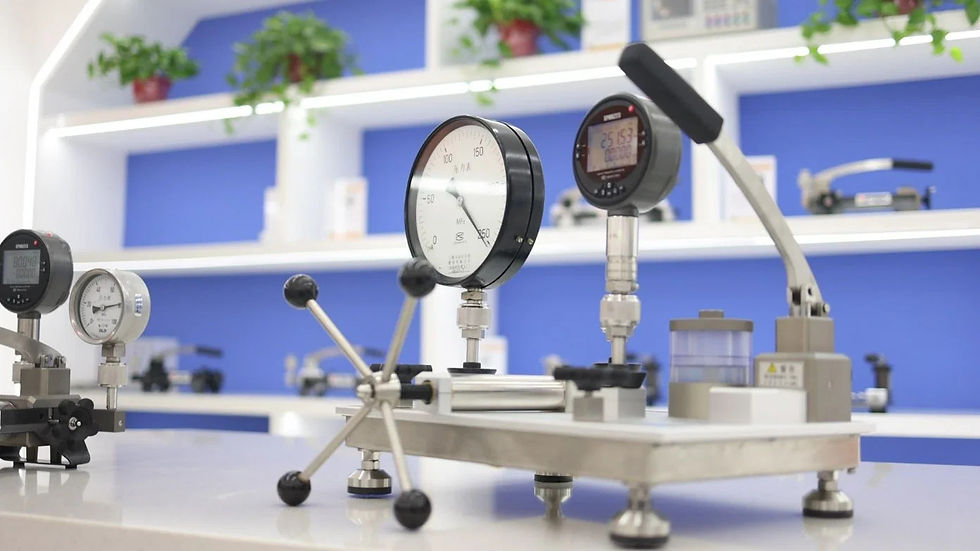
Benefits of Regular Calibration
Enhanced Accuracy: Regular calibration ensures that your pressure measurement devices provide accurate readings, which is essential for precise control and quality assurance.
Increased Reliability: Well-calibrated instruments are more reliable and less likely to fail, reducing downtime and maintenance costs.
Cost Savings: Accurate pressure measurements help prevent costly errors, reduce waste, and improve overall efficiency, leading to potential cost savings.
Regulatory Compliance: Meeting industry standards and regulations through regular calibration helps avoid legal issues and maintain your company's reputation.
Choosing the Right Calibration Service
Expertise: Select a calibration service with expertise in calibration. Ensure that they use accredited standards and follow industry best practices.
Accreditation: Look for calibration services that are accredited by recognised organisations, such as ISO/IEC 17025. Accreditation indicates that the service meets high-quality standards.
Equipment: Verify that the calibration service uses modern and well-maintained equipment to ensure accurate and reliable results.
Documentation: Ensure that the calibration service provides detailed documentation of the calibration process and results. This documentation is crucial for compliance and future reference.
Final Words
The calibration is a fundamental aspect of maintaining accuracy and reliability in pressure measurement devices. By understanding the importance of Thermometer Calibration and following best practices, you can ensure that your equipment operates effectively, meets regulatory requirements, and contributes to your operational success.
Whether you're in the manufacturing sector, healthcare, or any industry where pressure measurement is critical, regular calibration is key to achieving precise and reliable results. Invest in quality calibration services and maintain accurate pressure instruments to safeguard your operations and enhance overall performance.
Comments